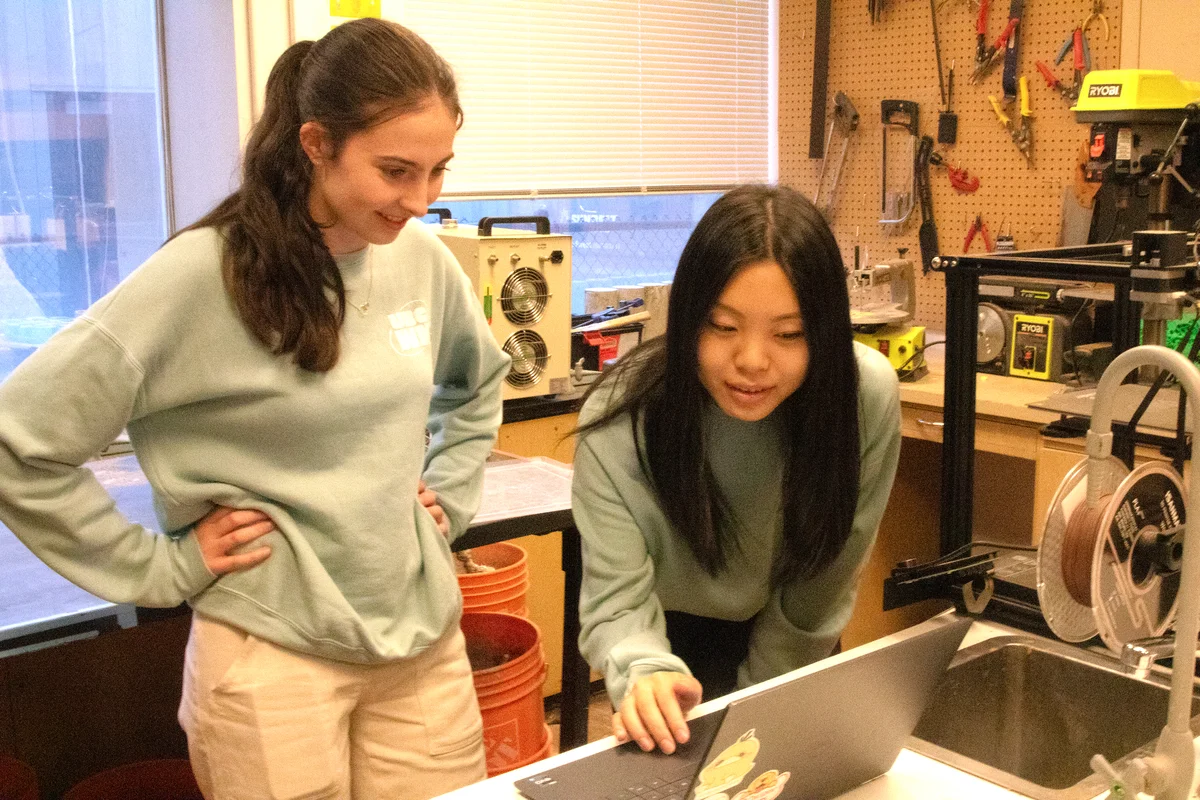
Imagine two plastic bags, drifting through the wind (wanting to start again). One of them will last forever, in a sense; breaking down into smaller pieces and continuing to pollute the oceans, fish and even the fossil record itself. The other falls apart completely on a chemical level; within a couple years, it’ll be as if it never existed.
Does the second sound impossible? Not if Jordan Thompson and Jasmin Fung of UBC’s Mycelium Mycopack project have anything to say about it.
The theory of biodegradable plastics
Plastics are a broad term and actually encompass many different types of materials. Famous examples include the PET used in plastic bottles, PVC used in insulation or pipes and polystyrene used in Styrofoam. They have varying properties and uses, but they all have one unfortunate thing in common: At a chemical level, they’re almost as indestructible as diamonds. You can break them down into smaller pieces, but they’ll still maintain their plasticky structure.
This has led plastics to become dubbed as ‘forever chemicals.’ Such chemicals have been found in everything from our food sources to the bottom of Marianas Trench and can have effects on health and wellbeing such as slowed child development.
Biodegradable plastics are different. They don’t just decompose into smaller and smaller pieces, they actually fall apart at a chemical level into pure organic material, the way a banana peel becomes compost.
That’s what the Mycopack project is aiming for.
Mycelium mycopacks
For now, the project is still in the early stages, with this year as the first design cycle.
“We’re going to be doing a lot of research, term one on exploring different mycelium strains that we want to use, and then term two, we’re going to start doing lab work,” said Fung.
“As a whole, we’re super passionate about sustainability, and also creating a circular economy,” Thompson said.
Thompson and Fung are upper-year engineering students, and between co-ops, social lives and courses, they’ve elected to lend some of their talents to the critical mission of finding a plastic that won’t be in the earth in 1 million years.
Before growing all the mycelium they need, they have begun planning what they need all their plastic to be able to do. It needs tensile strength (meaning, it can hold weight without breaking), it needs to be a good insulator, and it also needs to be waterproof.
“When you bake mycelium, usually after it grows into your desired shape, then you heat it up in an oven of sorts, and that makes it water resistant. But for fresh food packaging ... we’re not sure,” said Fung.
That’s really the worst thing about plastics: It’s so good at so many things, making it hard to transition to better alternatives.
Another problem is how mature and refined the plastic production process is. Manufacturers know exactly how much material to put into the machines, how long to heat it for and what temperature to use. If one wants to create a process for mycelium plastics, every single one of those things is going to have to be figured out.
Thompson and Fung did come up with a solution to their waterproofing woes: a coating that will reinforce mycelium’s water resistance, while still being fully compostable. They’re still hoping that mycelium itself will be sufficient, but even if not, they are confident that this is a problem they can solve.
Mycelium Mycopack is currently wrapping up its hiring process for the design team, and the extra power will help make all of these tasks a lot more manageable.
Still, that’s only one part. Thompson and Fung are both careful to keep expectations in check.
“It would be awesome if we could get it patented or have it as an actual product that people can use later on. But I think that’s something that’s going to take a lot more time,” Fung said. “I think our main goal is to just inspire people and also to educate others.”